In the industrial field, the use of agitators is essential for carrying out mixing and agitation processes in various sectors. There are different types of industrial agitators, but in this article, we will focus on the differences between mechanical agitators and industrial magnetic agitators.
What is a Mechanical Agitator?
Mechanical agitators are equipment that uses an external power source to generate an agitating movement in the container. This energy can come from electric motors, pneumatic motors, or hydraulic motors.
These agitators have a direct interaction with the product, which can increase friction and heat in the process. Some of the most common types of mechanical agitators are vertical and horizontal industrial agitators.
Mechanical agitators are particularly suitable for processes that require high levels of agitation, such as solid dispersion in liquids or homogenization of viscous mixtures.
They are also widely used in applications involving corrosive products. However, due to their direct interaction with the product, they can be affected by corrosion and require more regular maintenance.
It is necessary to lubricate and periodically replace the moving parts of these agitators to ensure optimal operation.
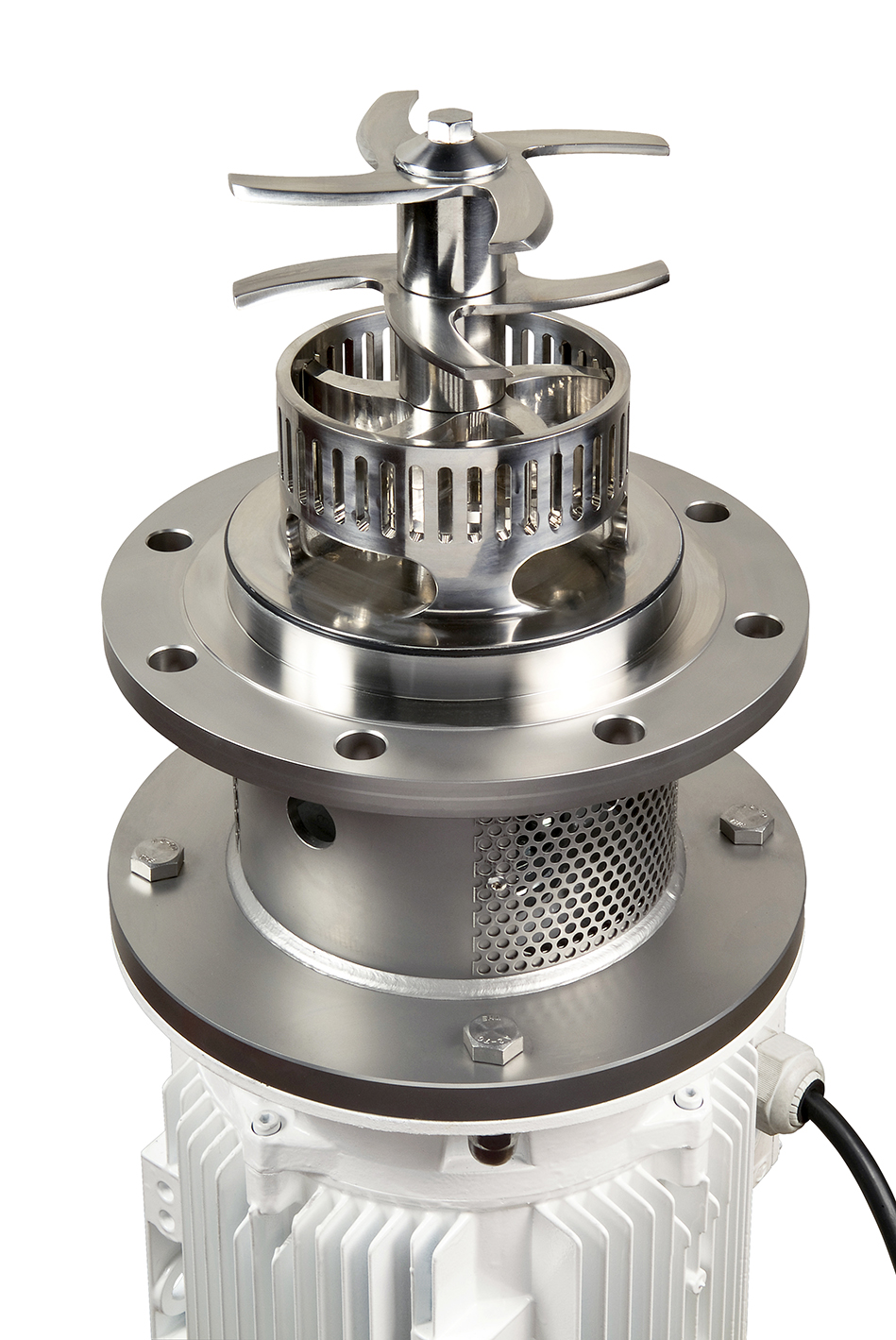
Our industrial agitators include:
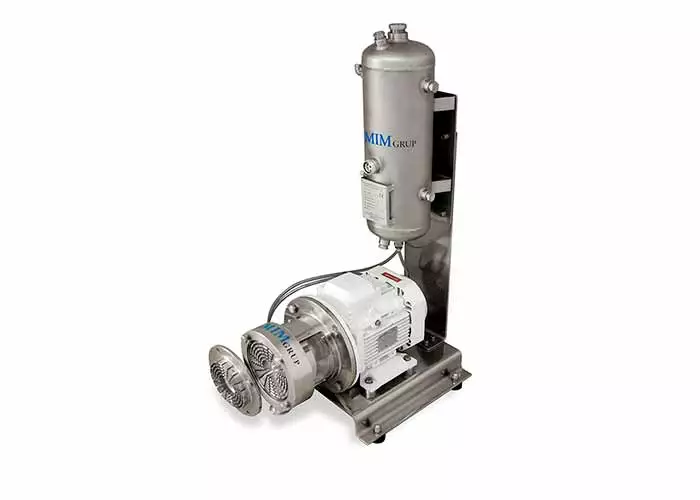
What is an Industrial Magnetic Agitator?
On the other hand, industrial magnetic agitators use a magnetic field to generate the agitating movement in the container. These agitators do not have a direct interaction with the product, which avoids additional friction and heat in the process. Their operation is based on a magnet placed outside the container and a magnetic impeller submerged in the liquid.
Magnetic agitators are ideal for processes that require gentle and precise mixing, such as chemical dissolution or suspension of shear-sensitive particles.
They are also particularly useful when working with corrosive products, as they are more resistant to corrosion than mechanical agitators. In terms of maintenance, magnetic agitators require less attention since they do not have exposed moving parts and do not require lubrication or periodic replacement of parts.
The 5 main differences between these two industrial agitators are:
In summary, mechanical and magnetic agitators are used in various applications according to the needs of each process. Mechanical agitators employ an external power source and have a direct interaction with the product, while magnetic agitators operate through a magnetic field and do not have a direct interaction.
Mechanical agitators are ideal for high agitation processes where corrosion is not a problem. On the other hand, magnetic agitators are more suitable for gentle and precise mixing, especially with corrosive products. Although magnetic agitators are usually more expensive, their efficiency and lower maintenance needs make them a beneficial long-term option.
Both types of agitators are available in different configurations and models to suit each application. Mechanical agitators can be vertical or horizontal, while magnetic agitators offer customized options. It is important to follow good operating and maintenance practices to ensure optimal performance and prolong the lifespan.
At InoxMIM, we offer a wide range of high-quality industrial agitators, along with advisory services and technical support. If you are looking for reliable and efficient agitators for your industrial processes, contact us today and discover how we can help you find the perfect solution for your needs!
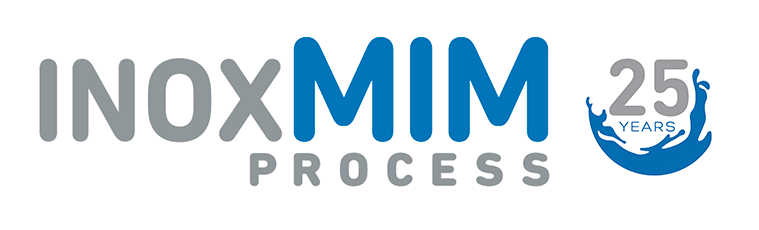