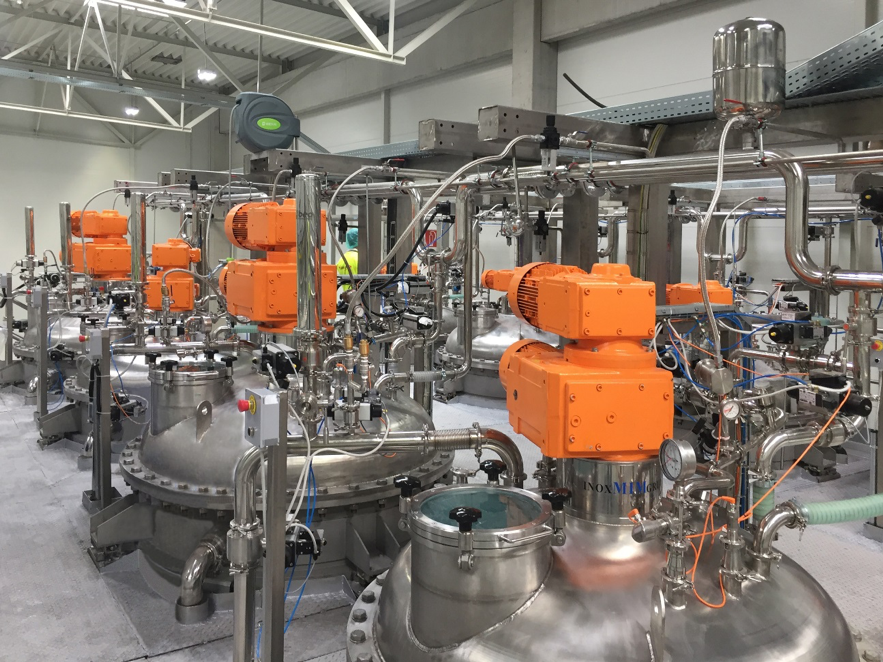
In this post, we will set out the steps to follow for proper maintenance of your cosmetics production equipment. After each use and/or when changing product, the units needs to be properly cleansed and flushed. There are factors that significantly affect the effectiveness of the system cleansing leading to increased risk of product contamination. Which are the most important?
Mechanical factor (agitation)
The design of the agitation and emulsion systems, curvature radius, accessibility, roughness and location directly influence the penetration of the cleaning products therefore the disinfection.
Time
In relation to the cleaning time, after a certain amount of time, the cleansing is complete, and any further system cleansing will have no added effect.
Temperature
We recommend working at a temperature of 80-85ºC for alkaline products and 60-65ºC for acid products. Each product has its optimum performance range and increasing the temperature does not necessarily increase efficiency. Excess temperature can generate unwanted chemical reactions that can render detergents inert.
Detergent
For each type of product there is a concentration at which the system cleansing is at maximum efficiency. Therefore, as concentration increases, so does the efficiency, however there is a ceiling above which efficiency starts to diminish. For this reason, dosing the detergents manually is not effective. If we fall short of the optimum concentration, more time is need for the cleaning process. If the concentration is too high, the product is being needlessly wasted.
Before starting a thorough cleansing of all your system parts, it is important to know what types of impurity there are, be they organic and/or mineral, and if the system cleansing requires a single phase or two-phase process in order to ensure the equipment is as clean as possible. Both types, on the whole, comprise three stages: Initial rinse, cleaning with detergent(s) and final rinse. When all the machinery is clean and ready to work again, you can start loading the reagents, bases, absorbents and components as normal. These basic guidelines are designed to clarify the maintenance process of your reactor.
What else should you know?
Always work safely and without taking any risks. Use respiratory protection if necessary, in addition to the other standard safety equipment for the area where you work. Keep in mind that chemical products and reactions can be harmful to your health. Don’t gamble with it.
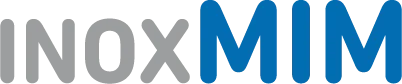
Have any more questions or doubts about the maintenance of your cosmetic reactor?
If so, or if you need a little more advice, please feel free to contact the InoxMIM customer service department. We have a technical service made up of highly-skilled professionals who will answer your questions about the maintenance of the reactors. Just remember that we have spent more than twenty-five years improving, maintaining and professionalising this specialist equipment for the cosmetic industry.
Since its humble beginnings in 1997, INOXMIM has always been heavily involved in the development and manufacture of industrial machinery. The pumping, agitation, mixing and fluid delivery systems that we manufacture have enabled us to meet the needs of our customers on a continual basis.
Through constant innovation and development, INOXMIM is able to provide complete solutions for most processes, whilst satisfying the most demanding industry requirements.
We are your ideal professional partner with a long history and a vast amount of experience.